Table of Contents
ToggleCoal handling plants (CHPs) are vital components of coal-based thermal power plants, responsible for receiving, processing, and transferring coal to bunkers for feeding the boilers. Let us know in detail about protection in coal handling plants and challenges.
Coal handling plants must operate efficiently to ensure a continuous supply of coal, avoiding disruptions that could halt the production of electricity. To maintain such operational efficiency, various protection systems, interlocks, and operating sequences are incorporated into the design and running of CHPs.
However, despite these protective measures, coal handling plants often face significant challenges related to operational and environmental factors.
Protections in Coal Handling Plants
Pull Cord Switch
- The pull cord switch is a critical safety mechanism, although it does not activate automatically. It must be operated manually by an operator when they detect a potential hazard or a severe disaster in the system.
- The primary benefit of the pull cord switch is that it can be engaged from any point along the conveyor belt. Operators must be vigilant in monitoring the belt’s condition and act promptly to prevent accidents that could cause extensive damage or injuries.
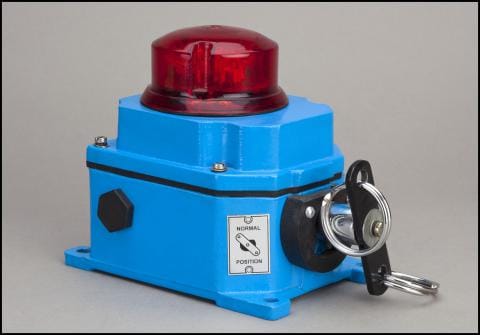
Belt Sway Switch
- Belt sway switches are mounted directly onto conveyor systems and are designed to protect the conveyor belts from excessive lateral movement, commonly known as belt sway. If a belt sways too far off its intended path, it risks wearing down its edges or becoming damaged.
- The belt sway switch detects this excessive movement and trips the system to halt the belt, preventing damage and ensuring the conveyor remains operational in the long term.

Zero Speed Switch
- The zero speed switch is a protection that operates when the conveyor’s speed drops below a predefined threshold. It automatically trips the system to prevent blockages at the transfer points and other components.
- The switch is typically located near the tail pulley and is essential in avoiding congestion and damage to the machinery.
Interlocks Provided in Coal Handling Plants
- Interlocks are crucial for ensuring the smooth and coordinated operation of multiple conveyor belts and systems within a coal handling plant. One of the key interlock mechanisms is the automatic tripping system.
- If one of the conveyor belts trips due to a malfunction or overload, all preceding belts and the associated vibrating feeders (used to transfer coal onto the conveyors) will also trip automatically. This ensures that coal does not continue to accumulate in the system, potentially causing hazardous blockages.
Operating Sequences of Coal Handling Plants
The operation of a coal handling plant involves three key sequences based on the availability of coal and the status of coal bunkers.
- Direct to the Bunker (Bunkering)
In this sequence, coal is received from various transportation modes such as railways or ropeways and transferred to the crusher system, where it is crushed to a size of approximately 25 mm. The crushed coal is then transported to the bunkers via conveyor belts and tripper trolleys. The feeding rate to the bunkers is controlled by electromagnetic feeders to match the boiler unit’s requirements. This process ensures a constant supply of fuel to the power plant’s boilers. - Direct to Stack (Stacking)
When the coal bunkers are full but coal continues to arrive via transportation methods, the coal is diverted to the coal stockyard. In this case, coal is either crushed or bypassed at the crusher house and then moved to the stockyard using stacking conveyors. Storing coal in the stockyard allows the plant to build a reserve supply that can be used during periods when coal transportation is unavailable. - Stacking to Bunkering (Reclaiming)
When coal in the bunkers is depleted and there is no immediate coal supply from transportation methods, coal from the stockyard is reclaimed. The reclaiming conveyors transport coal from the stockyard to the crusher, where it is processed and transferred to the bunkers. Automatic stacker cum reclaimers are often used for this process to optimize the stacking and reclaiming operations.
General Problems Faced in Coal Handling Plants
Despite the protective measures and interlocks in place, coal handling plants face several challenges that can disrupt operations:
- Design Problems
Coal received at power stations often has a lower calorific value and a higher ash content than the levels recommended by the plant’s manufacturers. This deviation from specifications results in overloaded systems, leading to reduced efficiency and low bunker fill rates. The high ash content also accelerates wear and tear on equipment, increasing maintenance needs. - Rainy Season Problems
During the rainy season, the coal becomes wet or muddy, leading to several operational difficulties. Wet coal can cause blockages in transfer chutes, particularly at input points where electromagnetic feeders operate. The formation of coal slurry in the coal yard further exacerbates these problems, resulting in frequent choke-ups and delays in coal transfer processes. - Miscellaneous Problems
- Snapping of Belts/Ropes: Conveyor belts and ropeway ropes are prone to damage due to jerks, overloading, or other stress factors. When belts or ropes snap, the entire system may need to be shut down for repairs, leading to considerable downtime.
- Derailment of Coal Wagons: When coal wagons derail, the unloading process is obstructed, preventing the timely unloading of subsequent wagons. This delay reduces coal availability and can result in financial penalties, such as demurrage charges from the railway department.
- Oversized or Muddy Coal: Oversized coal can damage conveyor belts, clog transfer chutes, and cause breakdowns in crusher rings. Additionally, muddy coal can create similar problems by sticking to machinery and clogging components, further complicating coal processing.
Conclusion
- Coal handling plants are essential to the functioning of coal-based power stations. They ensure a steady flow of coal to the boilers through a network of conveyors, crushers, and bunkers.
- However, the efficient operation of a coal handling plant depends on several protective systems such as pull cord switches, belt sway switches, and zero speed switches.
- Interlocks and defined operating sequences help streamline coal movement and prevent blockages or damage to the system. Despite these safeguards, CHPs encounter a variety of challenges, particularly related to the quality of coal, environmental conditions, and mechanical failures.
- Effective maintenance and adaptability in dealing with these issues are key to ensuring continuous and efficient operation.