Table of Contents
ToggleIn industrial settings, boilers play a critical role in generating the steam and heat required for various processes, from power generation to manufacturing. However, achieving efficient and complete combustion in boilers—especially when dealing with different types of fuel like coal, oil, or gas—requires a precise understanding of the principles behind fuel firing.
This blog, Fuel Firing in Boilers, dives into the science and mechanisms of boiler firing systems. We’ll explore the types of boilers used across industries, key components essential for smooth operation, and the different methods employed to fire fuels effectively.
From coal-fired systems to modern oil burners, understanding the nuances of various fuel firing techniques can significantly enhance boiler efficiency, reduce costs, and improve environmental performance. Whether you’re looking to enhance boiler operations or just want to understand more about industrial combustion, this comprehensive guide will provide valuable insights into the principles, practices, and advancements in fuel firing.
Types of Boilers
Boilers are categorized into three main types, each with specific applications:
Boiler Type | Description | Typical Use |
Fire Tube Boiler | Has hot gases flowing through tubes, surrounded by water | Commonly used in locomotive engines |
Water Tube Boiler | Contains water in tubes with hot gases surrounding them | Primarily used in power stations |
Forced Once-Through/Mono Tube Boiler | Steam generator without water storage, forcing water through tubes directly | Often used as a marine boiler |
Boiler Components
A boiler system consists of several critical components:
- Drum: The main reservoir for water and steam.
- Down-Comers: Carry water from the drum to the lower parts of the boiler.
- Feeder Tubes & Headers: Distribute water evenly across the boiler.
- Riser Tubes: Return heated water from lower parts to the drum.
- Primary & Secondary Superheaters: Heat steam to higher temperatures.
- Economizer: Preheats feed water using residual heat from flue gases.
- Furnace: Where fuel is burned to generate heat.
- Air Pre-Heaters: Preheat the incoming air to boost combustion efficiency.
- Auxiliaries: Include fans (forced draught, induced draught, primary air fans), coal mills, coal feeders, burners, and ash removal and disposal units (e.g., electrostatic precipitators, ash extractors, pressure conveyors).
Principles of Efficient Combustion
Efficient combustion in boilers depends on managing three critical factors: Temperature, Turbulence, and Time (the Three ‘T’s).
- Temperature
The fuel must reach its ignition temperature to ignite. For coal, the ignition temperature ranges between 400°C and 425°C. Maintaining the correct temperature is vital, as it affects the combustion rate; a slight temperature increase can accelerate combustion, while a decrease may slow it down or even extinguish the flame.
- Turbulence
Turbulence helps fuel particles to quickly and thoroughly contact oxygen molecules, enabling rapid and complete combustion with minimal excess air. Excess air beyond optimal levels results in unnecessary heat loss through the chimney.
- Time
Adequate time is required for complete combustion, depending on the fuel particle size. The design of the furnace and the firing type ensures that enough time is allowed for combustion, which is also influenced by turbulence and temperature.
Methods of Fuel Firing in Boiler
Coal Firing
- Stoker Firing: Although not widely used in high-capacity boilers today, many stoker-fired boilers are still operational.
- Coal Size: ¾” – 1″.
- Primary Air: Admitted under the fuel bed to maintain ignition temperature.
- Coal Bed Layers:
- Top Layer (Distillation Zone): Volatiles are released and burned in secondary air, creating some turbulence.
- Middle Layer (Reduction Zone): Carbon and coke burn to form CO₂.
- Bottom Layer: Volatiles pass through the fuel bed, with CO₂ reduced to CO due to limited oxygen. Secondary air above the bed completes combustion.
- Control Mechanism: Combustion can be controlled by adjusting grate speed and air flow. Uniform fuel bed thickness is crucial for consistent combustion.
- Pulverized Fuel (P.F.) Firing:
- Increases fuel surface area, speeding up combustion and releasing volatiles.
- Types of P.F. Firing:
- Vertical or Down-Shot Firing: Ideal for low volatile coals; secondary air is introduced gradually to enable longer flame combustion.
- Horizontal Firing: Suitable for bituminous coals with high volatiles, using short flame burners for faster combustion. In long-flame tangential firing, combustion is completed in a turbulent “fireball” for efficiency.
Oil Firing
Oil firing is a crucial method for generating heat and steam in thermal power plants, particularly during startup, peak load demands, or as a backup to coal-fired systems.
In oil-fired systems, fuel oil is burned in specialized burners where it is atomized into a fine mist, ensuring better mixing with air for efficient combustion. Proper atomization is essential as it increases the fuel surface area exposed to oxygen, leading to faster and more complete combustion.
Boilers typically begin ignition using a High-Speed Diesel (HSD) or Light Diesel Oil (LDO) igniter, where oil is atomized by pressurized air, and a high-voltage spark establishes the flame. Pilot torches, which ignite the main burners, help sustain coal flames in adjacent burners.
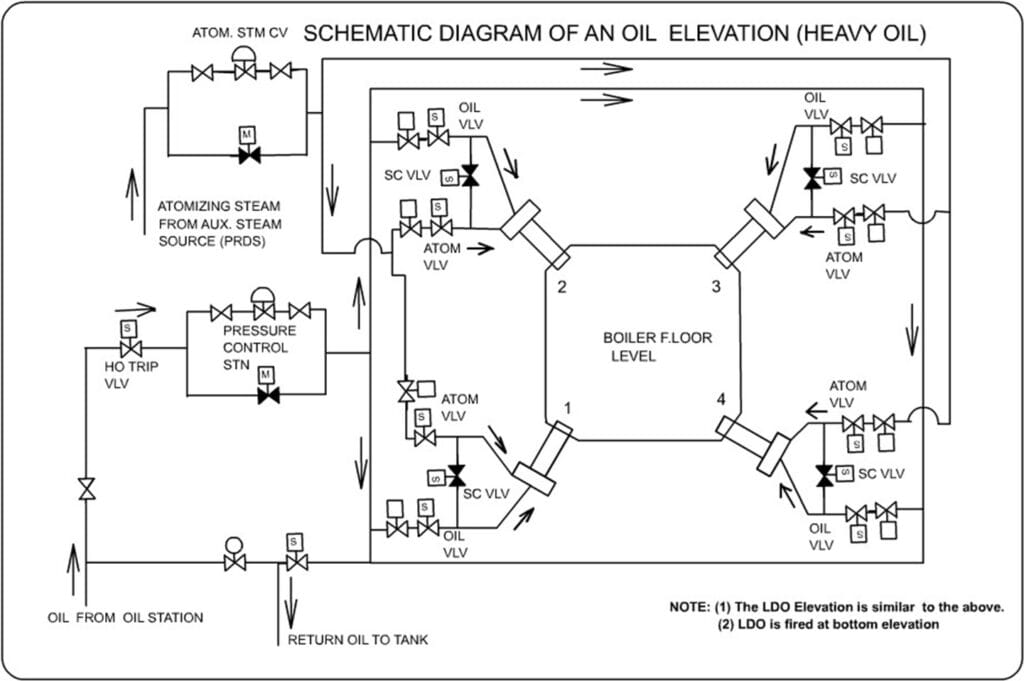
Oil Burners and Atomization Methods
Atomization involves breaking oil into fine droplets for efficient combustion. There are various atomization techniques:
- Mechanical or Pressure Atomization: High-pressure oil exits through a nozzle, forming a fine spray. Requires an oil viscosity of 80-120 Redwood seconds and pressures of at least 14-16 kg/cm².
- Steam Atomization: Steam intersects oil at a slightly higher pressure, improving atomization. Allows for a lower pressure threshold (5 kg/cm²) and a turn-down ratio of 10:1.
- Air Atomization: Similar to steam atomization, using air instead of steam for smaller installations.
- Spinning Cup Burner: Primarily used for very small setups.
Oil Burner Installation
- Air Register: Controls secondary air flow and induces a swirl for better air-oil mixing.
- Burner Throat: A convergent-divergent shape for improved air direction towards the flame.
- Diffuser: Protects the flame from excessive air and aids in achieving swirl, ensuring good combustion.
Ignition Temperatures of Fuels
Fuel Type | Ignition Temperature (°C) |
Bituminous Coal | 408 |
Semi-Bituminous Coal | 466 |
Anthracite | 496 |
Acetylene | 482 |
Ethylene (C₂H₆) | 538 |
Hydrogen | 610 |
Methane | 650 |
Carbon Monoxide (CO) | 654 |
In it something is. Clearly, many thanks for the help in this question.