Table of Contents
ToggleCoal feeders are essential components in power plants, responsible for regulating the coal supply to coal mills. Their operation directly impacts the efficiency of boilers by controlling the load and maintaining the required pressure.
In this article, we delve into the types of coal feeders, their components, working mechanisms, and speed control techniques to provide a holistic understanding of their role in thermal power plants.
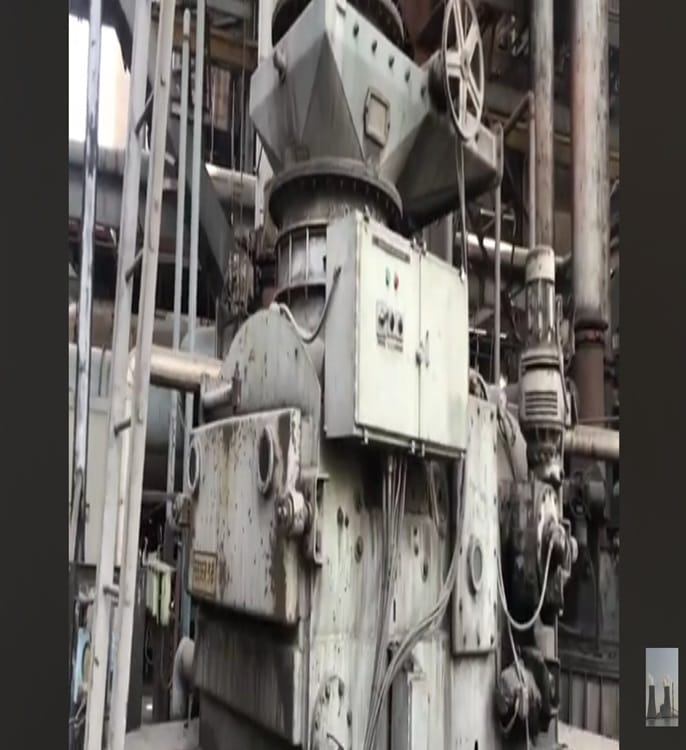
Types of Coal Feeders
Coal feeders are primarily classified into two types:
- Drag-Chain Type Feeder:
This type uses a chain mechanism to move coal from the hopper to the mill. The coal bed thickness can be adjusted for flexibility, allowing better control over feeding without extensive speed variation. - Rotary Type Feeder:
A rotary feeder rotates to deliver coal to the mill. For example, a “100 lb rotary feeder” delivers 100 pounds of coal per revolution. These feeders are widely used due to their simplicity and reliability.
Key Components of a Raw Coal Feeder
A raw coal feeder, particularly of the volumetric type, consists of several parts designed to ensure safe and efficient operation:
- Feeder Body:
The body of the feeder is equipped with a provision for seal air to prevent air leakage and maintain system efficiency. - Inspection Doors and Gates:
Includes isolating gates, rod gates, and spring-loaded flap gates to facilitate inspection and maintenance. - Protective Shear Pin:
This safety device breaks under excessive load, stopping the feeder and protecting it from damage due to foreign material. - No-Coal Flow Device:
Alerts the operator in case coal flow is interrupted, ensuring prompt corrective action. - RPM Indicator:
Displays the feeder’s operating speed, enabling precise adjustments as needed. - Air Cut-Off Solenoid:
Used in feeders with Positive Infinitely Variable (PIV) gearboxes, it isolates air supply during maintenance or emergencies. - Seal Air to Shaft Glands:
Prevents air ingress around the rotating shaft, ensuring smooth operation.
Maintenance Safety Precautions
Important: Before performing maintenance on raw coal feeders, the following precautions must be observed:
- Turn off the Primary Air (P.A.) fan to prevent pressurized air from affecting the system.
- Ensure that inspection doors, hot and cold air gates, and dampers are securely closed to avoid hazardous situations.
Principles of Speed Control in Coal Feeders
The speed of coal feeders directly influences the mill’s loading and performance. By adjusting the speed, operators can control the quantity of coal supplied to the mill. The two primary speed control mechanisms for coal feeders are:
P.I.V. Drive (Positive Infinitely Variable Drive)
- In a PIV drive system, a constant-speed induction motor is coupled to the feeder through a PIV gearbox.
- The speed can be varied by adjusting the distance between two wheels (W1 and W2) in the gearbox. This adjustment alters the output speed from N1 to N2.
- PIV drives are reliable and offer precise control, making them a popular choice in rotary feeders.

Eddy Current Couplings
- Eddy current couplings work on the principle of magnetic flux. An AC motor drives the input shaft at a fixed speed, while the output shaft’s speed is adjusted through the magnetic flux coupling.
- Increasing or decreasing the magnetic flux density changes the slip between the input and output shafts, thereby varying the speed.

Operating Principle of Eddy Current Couplings
Eddy current couplings are designed for efficient and responsive speed control. Their operation involves the following steps:
- Current Sensing and Comparison:
A current sensing device measures the coil current, which is compared to a pre-set value. - Load Adjustment:
When load demand increases, the coil current rises proportionally, ensuring the output shaft maintains the desired speed. - Overload Protection:
If the load exceeds the safe limit, the system triggers an “OVERLOAD FAULT” alarm and activates a potential-free contact for annunciation. The fault condition is latched until acknowledged and resolved. - Manual Reset:
Operators can reset the system using the reset button on the panel. However, if the fault persists, the condition reappears upon releasing the button, indicating that corrective action is still required.
Advantages of Coal Feeder Speed Control Mechanisms
- Efficiency:
By controlling the coal flow rate, feeders ensure optimal mill loading and boiler efficiency. - Flexibility:
Speed variations allow operators to adapt to changing load requirements. - Safety:
Protective features like shear pins and overload alarms safeguard equipment from damage. - Energy Savings:
Precise control minimizes energy wastage, especially in systems with eddy current couplings, where slip energy is dissipated as heat.
Additional Features in Drag-Chain Feeders
Drag-chain feeders provide added flexibility by allowing coal bed thickness adjustments. This feature complements speed variation by offering another dimension of control over coal feeding rates.
Challenges and Maintenance Considerations
While coal feeders are robust, they are subject to wear and tear due to the abrasive nature of coal. Common challenges include:
- Obstruction:
Foreign materials in coal can cause blockages. Regular inspection and maintenance can mitigate this issue. - Component Wear:
Parts like chains, shear pins, and seals require periodic replacement to maintain performance. - Calibration:
Feeder speed control systems must be calibrated regularly to ensure accuracy.
Conclusion
- Coal feeders are indispensable in power plants, ensuring the smooth and efficient supply of coal to mills. With advanced speed control mechanisms and robust safety features, they play a pivotal role in maintaining boiler performance and system reliability.
- A comprehensive understanding of their components, operation, and maintenance is essential for optimizing their performance and extending their lifespan.